Variable Frequency Motor Drives
- David Peterson
- Jul 1, 2020
- 3 min read
There is a wide variety of motors used for industrial equipment including both DC and AC, but the 3-phase synchronous AC motor is the most common for large, heavy-duty applications.
The original method of driving motors was limited to on/off contactors and switches - they're cheap, simple, and they don’t use much power.

The first improvement to this basic control included a softer starting system that used variable resistances, or preferably solid-state devices like transistors to provide a slower startup/down (called ‘ramp’) time.
Further evolution of digital control systems led to the device we now call a Variable Frequency Drive (or VFD).
This new control ability is far beyond simply controlled ramp times.
Top speeds, accelerations, temperatures, as well as current and voltage monitoring - these are just a few examples of some of the control and feedback values available for these drive units.
To supply power to the VFD, there are two options, single- or three-phase.
Single-Phase (or 1φ) AC power is a supply for VFDs that power only relatively small motors.
Single-phase power is usually only a small voltage (120 or 240), so to deliver greater power to motors, the current must be higher. Single-phase wiring found in residential or commercial structures simply cannot handle the large currents.
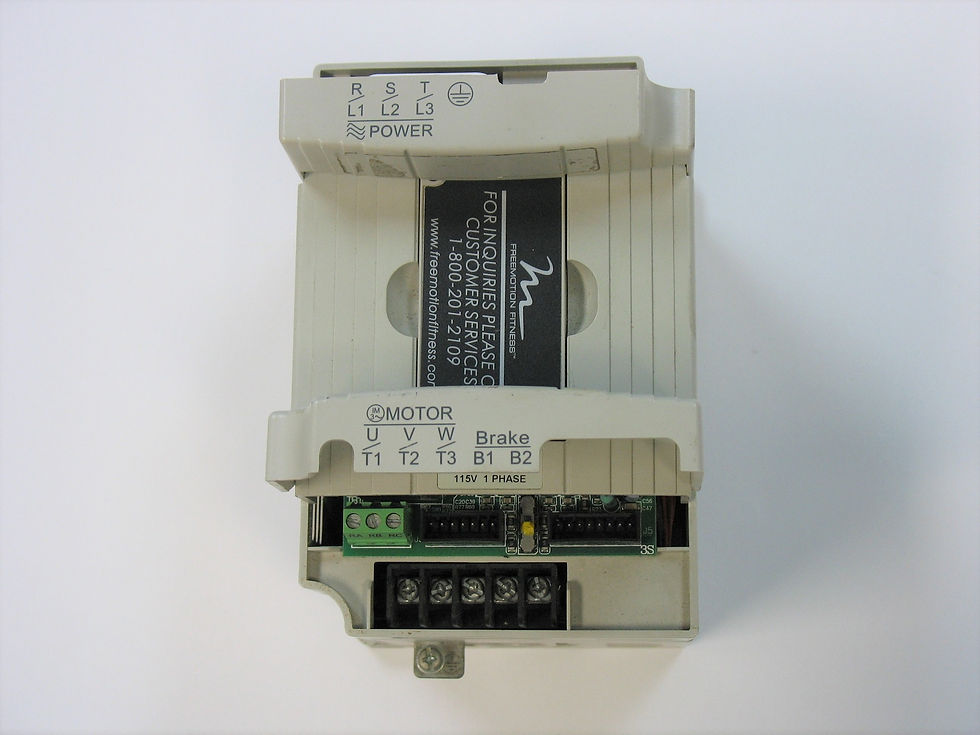
Three-Phase (or 3φ) AC is a common industrial voltage supply. The power grid is designed to supply much more current at higher voltages to these kinds of systems, so it’s the logical choice (and really the only choice) if high power motors must be used.
But for output, it's 3φ.
It’s always 3φ.
But hold on, before it becomes too easy, there is still some variation!
3φ still can have higher and lower voltages.
Some VFDs, especially those with single-phase supplies, can only output low voltage 3-phase. This is ideal for motors wired for 208-240 volts.
For larger VFDs supplied with 3-phase inputs, the output voltage can be either in the lower 208-240 range, or up in the higher 277-480 range.

In many small systems, only a couple of simple controls are required, like one button to start and another to stop, and maybe a run/jog selection.
In these cases, it’s cost-effective to just wire the buttons to the I/O terminals on the VFD.
Most modern VFDs are driven by commands from a network interface, like ethernet, provided by a PLC.
Ethernet is the most common, but others that are commonly used are serial RS-232, or RS-485 networks that send data in a Modbus or CAN Bus structure (similar to the engine computer in a car).
Although they are often built right onto the unit, it's common for manufacturers to assume that the customer will have a specific need.
They don’t want to include every possible type of port in every drive unit. Instead, they provide a wiring harness and the customer must purchase a signal board that fits their specific needs to plug in the wiring harness.
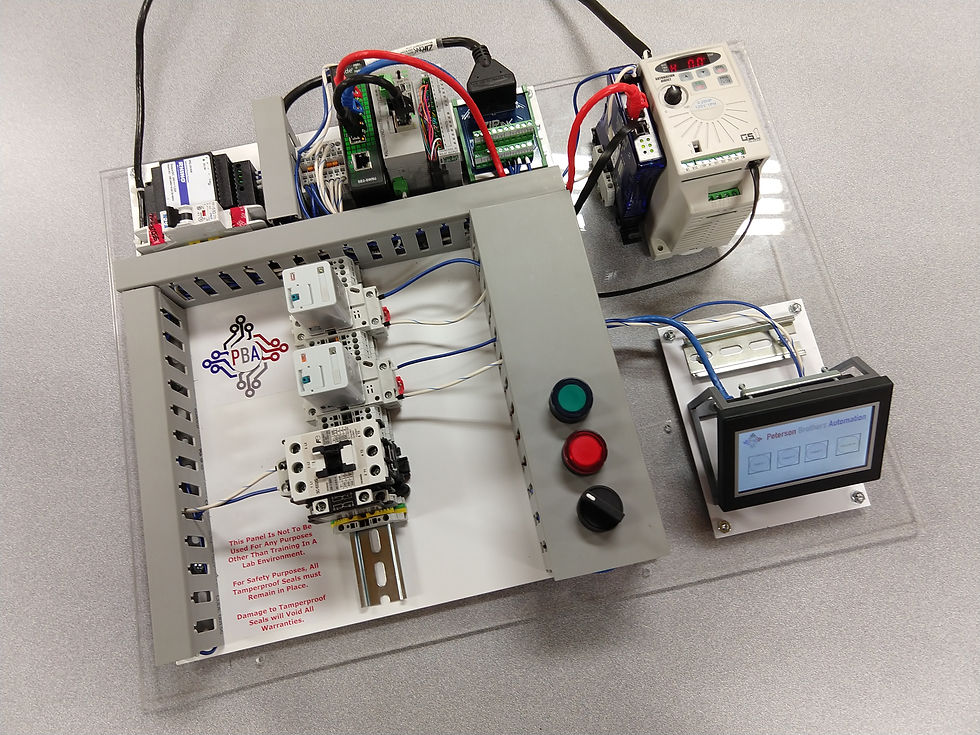
The purpose of the VFD really is quite simple – driving a 3-phase electric motor.
But there's a lot more to driving motors than just turning it on and off.
Oh if only life was that simple...
Both our classes and our training panels can teach what you need to know about 3-phase motor control.
We love motors, and we love working with VFDs. We'd like to be on your team, enabling you to learn this equipment as well!
コメント